Highlights of Measuring Dielectrics With RF Equipment Part 3
by Peter McNeil | Feb 01, 2023

In the previous blogs in this series, the basics of dielectric measurement with RF equipment was discussed. This also included a highlight of two common methods of dielectric characterization using VNAs, transmission/reflection line method and Open-ended coaxial probe method. This section provides more insight into the free space method and resonant methods. Like other dielectric measurement methods, the methods described here make use of VNAs, Coaxial Cable Assemblies, High-speed End Launch Connectors, Coaxial GS/GSG Probes and Probe Positioner, various Waveguide hardware, and Waveguide Antennas.
Related articles

Peter McNeil | Jun 13, 2024 | RF Cable Assemblies
There are several commonly used methods of carrying electromagnetic energy along conductive pathways. The most common of which for RF applications are RF cable assemblies, such as coaxial cable or twisted pair. The better shielding and lower loss capability of coaxial cable means that for frequencies over a couple hundred-megahertz, coaxial cable assemblies are the most commonly used for high frequency applications from hundreds of megahertz to over 110 GHz. These cables are used in virtually every RF application, from home fixed wireless access to space communications. There are RF cable assemblies made for every environment RF equipment is used, including automotive, train/rail, marine/naval, aerospace, military/defense, and commercial.
RF coaxial cable assemblies are composed of three separate components and the method of attachment between the components. Each coaxial cable assembly has a coaxial cable and two coaxial connectors. The coaxial connectors need to be compatible with the coaxial cable, but not necessarily the same coaxial connector type. A coaxial cable assembly needs to be attached, or otherwise manufactured, in such a way that the coaxiality of the transmission line is maintained throughout the assembly. Coaxiality refers to the alignment of the inner conductor of the cable or connector and the outer shielding of the cable or connector. In some cases, a RF cable assembly may have a connector that is not a coaxial connector, but instead a banana connector or even exposed center conductor for specific use cases.
Coaxial Cables typically have a center conductor, dielectric spacer, an outer conductor, and an outer cable jacket. There may be a variety of additional layers to enhance environmental protection, physical ruggedness, or to enhance electrical performance. Though the most common type of coaxial cable found as cable assemblies is flexible cable, or flex cable, there is also rigid and semi-rigid coaxial cable. These cables tend to exhibit better electrical performance than flexible coaxial cables at the cost of less physical flexibility and the flexibility to be used in a variety of applications. RF Cables may have one of a variety of different connectors, the most common of which are threaded coaxial connector types, such as SMA, N-type, 4.3-10 DIN, 3.5mm, etc. There are also several common types of coaxial connectors that are push-connect, such as SMP, MCX, MMCX, QMA, and others. Bonnet style fittings are also common but are limited in frequency to 2 GHz. Different connectors can be used for each end of the coaxial cable assembly, but it is important to note that the maximum frequency of the cable, and many other of the electrical performance parameters, will be limited by the lowest rated of the coaxial cable assembly components
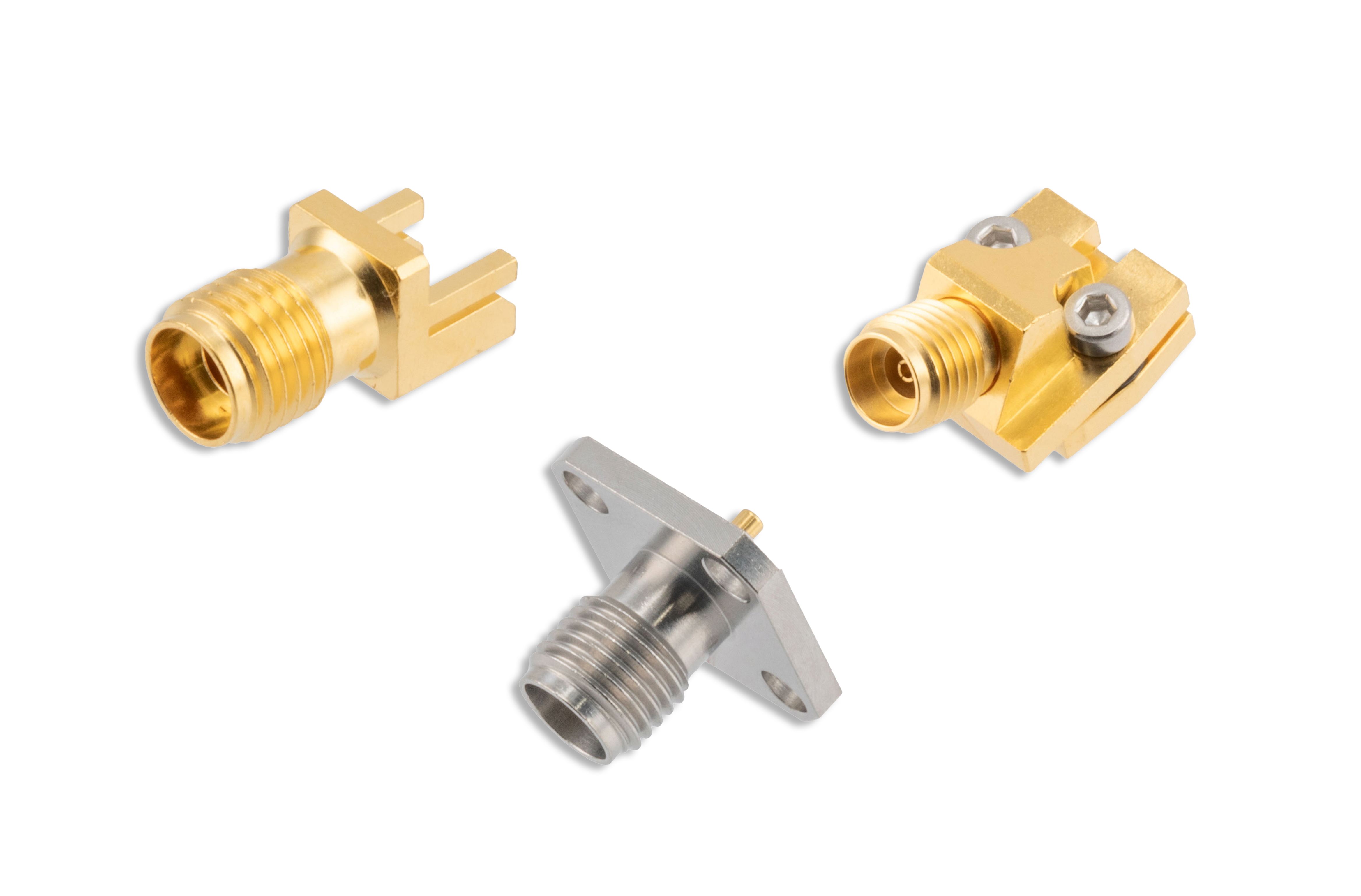
Peter McNeil | Feb 13, 2025 | RF Interconnects
Designing high-performance RF systems often requires overcoming space limitations and optimizing signal routing with specialized components, such as angled PCB connectors. Unlike traditional straight connectors, PCB connectors allow for a more flexible orientation, making them ideal for compact designs where efficient use of space is crucial.
For example, when prototyping or working with tight spaces, the 1.85mm, female PCB mount vertical launch connector offers a clamp attachment design for easier installation. This product in particular supports up to 67 GHz performance, making it a reliable option for applications requiring high-frequency signal transmission.
Angled connectors like this one not only optimize space but also ensure that your system maintains low signal loss and high-frequency integrity, even when space is at a premium. Whether you're working on satellite communications, aerospace systems, or military radar systems, choosing the right connector can significantly enhance system performance.
Similarly, for applications requiring high-frequency performance and easy integration, products like the 2.4mm Jack PCB Mount End Launch and the 2.4mm Jack Solderless PCB Mount offer solutions that streamline installation and improve overall system reliability. With 50 GHz performance and minimal signal loss, these connectors are designed to meet the rigorous demands of high-performance systems.
How to Choose the Right Printed Circuit Board Connectors for Your Application
Selecting the appropriate RF PCB connectors for your system requires careful consideration of several factors, including the frequency range, VSWR (Voltage Standing Wave Ratio), mounting options, and the available space in your design. Each of these factors plays a crucial role in ensuring the efficiency and performance of your RF system.
· Frequency Range: The frequency range is one of the most important factors when choosing a connector. RF connectors that support up to 50 GHz, are ideal for applications that demand high-frequency performance. It's essential to select connectors that match the frequency requirements of your system to avoid signal degradation and ensure the integrity of your data transmission.
· VSWR: VSWR is an important indicator of signal integrity. A low VSWR ensures minimal signal loss, meaning your system can transmit signals with high efficiency. When evaluating connectors, always check the VSWR specifications to ensure they meet the requirements of your application.
· Mounting Options: The mounting method of your connector can have a significant impact on the ease of installation and the overall design of your system. End-launch connectors are excellent for systems where space constraints require a compact and efficient connector without sacrificing performance.
· Available Space: The physical space available in your design is another critical factor to consider. For systems with tight space requirements, narrow-body connectors high performance while occupying minimal space. These types of connectors are ideal for applications in military defense or satellite communications, where every inch of space matters.
Optimizing System Performance with the Right Connectors
Choosing the right connector can dramatically impact the performance of your RF system. For industries such as military defense, satellite communications, and RF testing, where precision is critical, high-performance connectors are a must.
These connectors also provide flexibility in routing and space-saving benefits that are essential in modern RF designs. Whether you need angled connectors for tight spaces or end-launch connectors for ease of integration, the right product ensures your system will operate at its best.
Future-Proof Your RF Designs with Top-Quality Printed Circuit Board Connectors
When designing your next high-performance RF system, consider the impact that these connectors and end launch connectors can have on your system’s performance. The connectors discussed here offer high-frequency performance, low-loss transmission, and the versatility required for demanding applications. Whether you’re working in telecommunications, military defense, or test & measurement, choosing the right connector ensures your system operates efficiently, even in tight spaces.
Our PCB connectors provide optimal signal integrity, reduced installation time, and ensure your systems perform at their best. Explore our range of high-performance RF PCB connectors today and get the reliability you need for your next big project.
Peter McNeil | Sep 14, 2022 | Waveguide Terminations
A waveguide termination, or waveguide load, is a common waveguide component found in many RF systems, including radar, test & measurement, satellite communications, and aerospace communications. Similar to how RF coaxial terminations work, waveguide terminations absorb excess RF energy that enters the termination.
Waveguide Termination
Terminating a waveguide can be useful for a variety of reasons. For instance, with switching radar, if the transmitter needs to be switched off there will be some time before the high-power transmission devices can be deenergized. During this time period the transmission energy can be switched to a high-power waveguide load that safely absorbs the energy instead of the high-power RF signal energy being reflected back to the transmission devices or receiver devices. Another example is the termination of a directional coupler’s ports to realize certain configurations or enhance the coupler performance.
A waveguide termination is basically a waveguide flange, a waveguide, RF absorbing materials, and some form of thermal management/heat dissipation. The waveguide body is generally made of the same material as the termination heat sink and is commonly brass or aluminum but could be made of other engineering metals depending on the application. The RF absorbing material is often refractory ceramics, or some other stable RF absorbing material that can handle the high temperatures associated with absorbing RF engineering and effectively transfer the thermal energy to the thermal management features of the termination.
Depending on the power requirements, waveguide size, and other factors, there are several common options for waveguide thermal management. The most common for relatively low power terminations are just a straight body waveguide with the waveguide body being the RF absorber encapsulation and thermal management using passive cooling. Higher power waveguide loads can be designed with heat sink fins or even active cooling measures. Forced air cooling is the more common active cooling method used with waveguide terminations. However, liquid-cooled/water-cooled systems do exist for extremely high-power RF terminations. Another choice is to have a water coupled system, where water, or a water glycol mixture, is used as the RF absorbing material and thermal management transfer fluid.
The main electrical performance and features of a waveguide termination are frequency range (waveguide size), VSWR, and input power handling. Physical performance features, such as size, weight, and material are also significant concerns in many applications. Waveguide terminations are often plated or coated to prevent corrosion (passivation) and may also be additionally painted for enhanced environmental protection and thermal management considerations.